In industries where precision and safety are paramount, accurate pressure measurement is essential. From mining and oil & gas to food and beverage processing, pressure gauges are used to monitor and control various processes, ensuring systems operate safely and efficiently. But with so many types available, choosing the right pressure gauge for specific applications can be challenging. So, what are the 4 types of pressure gauges, and what are their unique advantages? In this article, we’ll explore Bourdon tube, diaphragm, capsule, and digital pressure gauges, offering a clear guide to their workings, benefits, and industry applications.
Bourdon Tube Pressure Gauge
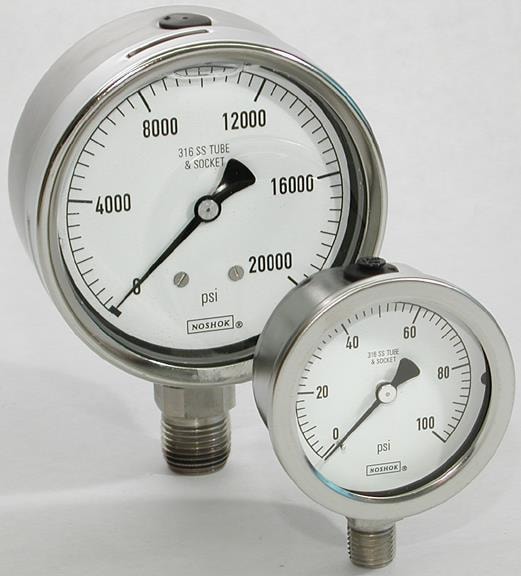
The Bourdon tube pressure gauge is one of the most widely used types of pressure gauge. It operates on a simple yet effective principle: a curved tube inside the gauge straightens as pressure increases. This movement is translated into a rotary movement, which turns a pointer on the gauge face, providing a clear and immediate pressure reading. Bourdon tube pressure gauges are available in various configurations, including brass and stainless steel, to suit different media and environments.
Advantages of Bourdon Tube Pressure Gauges:
- Durability: Bourdon tube gauges are robust and can withstand high pressures, making them ideal for industrial applications.
- Versatility: These gauges are suitable for both gaseous and liquid media, as long as the media isn’t highly viscous or crystallising.
- Wide Pressure Range: With pressure ranges up to 7,000 BAR, Bourdon tube gauges are a reliable choice for high-pressure systems.
Common Applications: Bourdon tube pressure gauges are commonly used in industries like mining, oil & gas, and manufacturing, where durability and reliability are critical. Their ability to handle high pressures makes them ideal for heavy-duty industrial processes.
Diaphragm Pressure Gauge
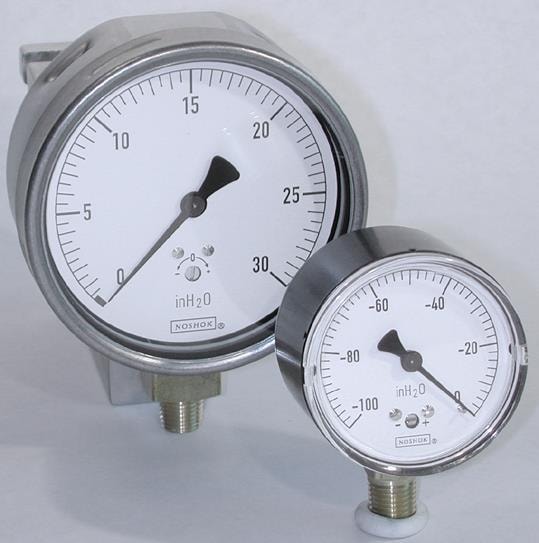
Diaphragm pressure gauges measure pressure using a flexible membrane, or diaphragm, which expands or contracts as pressure is applied. This movement is transferred to the gauge needle, allowing for accurate readings even at low-pressure ranges. Diaphragm gauges are well-suited for applications where the media may be corrosive or viscous, as the diaphragm can be coated with protective materials.
Advantages of Diaphragm Pressure Gauges:
- Corrosion Resistance: The diaphragm can be lined with materials like PTFE, making these gauges suitable for aggressive media.
- Low-Pressure Sensitivity: Diaphragm gauges provide accurate readings at lower pressures, where other gauges may struggle.
- Adaptable to Special Media: Diaphragm pressure gauges are capable of handling viscous or contaminated media effectively.
Common Applications: Industries such as food and beverage, chemical processing, and pharmaceuticals rely on diaphragm pressure gauges for applications requiring high sensitivity at low pressures. Their corrosion resistance makes them ideal for processes involving aggressive chemicals or reactive substances.
Capsule Pressure Gauge
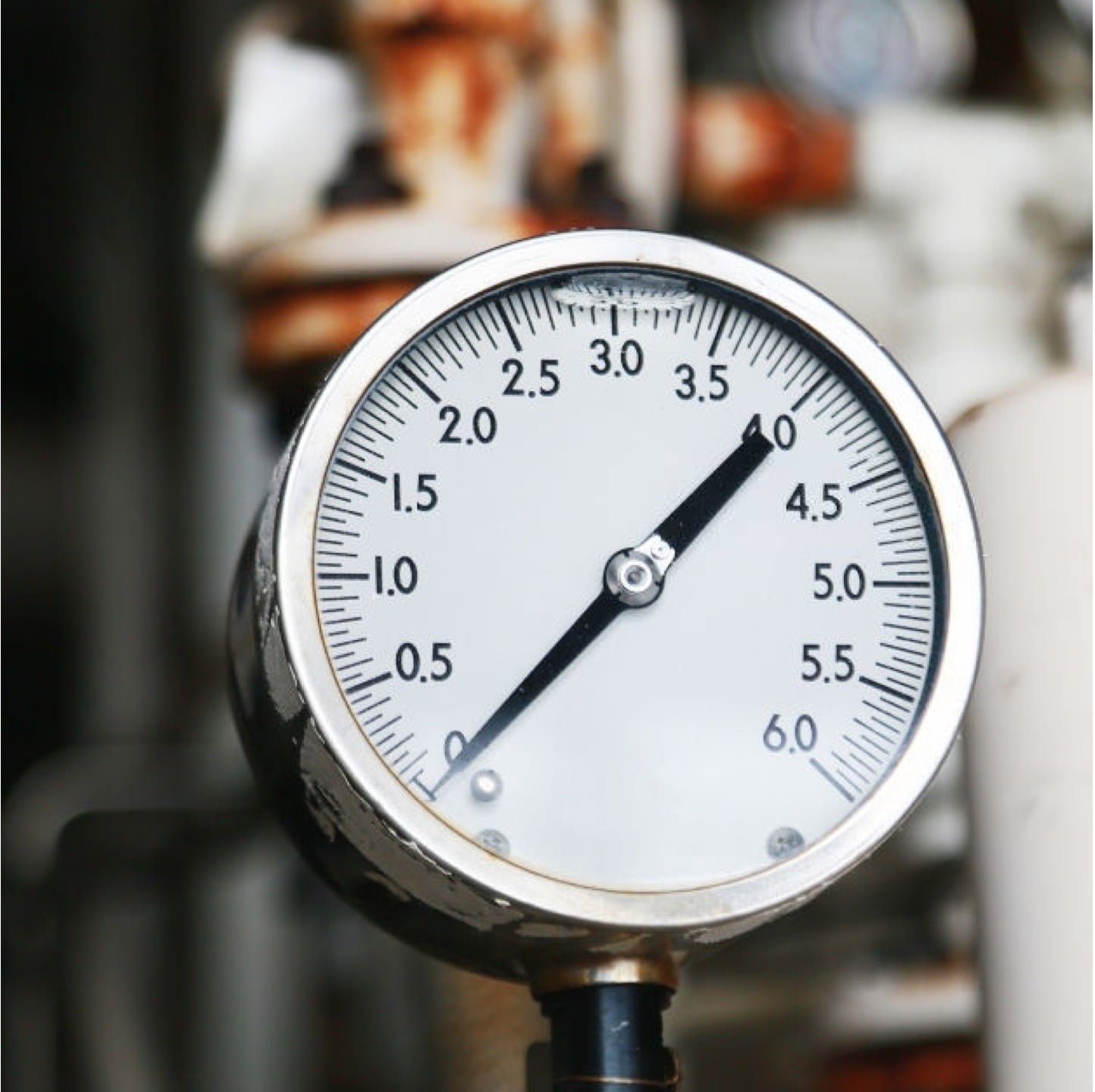
Capsule pressure gauges are specifically designed for low-pressure applications, particularly in gaseous media. The gauge consists of two circular, corrugated diaphragms joined around the edges. As pressure is applied, the capsule expands, creating a movement that is transferred to the gauge pointer. Capsule gauges are known for their high accuracy and are typically used in applications where precise low-pressure readings are necessary.
Advantages of Capsule Pressure Gauges:
- High Accuracy at Low Pressures: Capsule gauges are optimised for measuring low pressures with excellent precision.
- Compact Design: These gauges are often smaller and easier to install in confined spaces.
- Specialised for Gaseous Media: Capsule gauges excel in low-pressure gas applications, offering reliable readings without risk of media contamination.
Common Applications: Capsule pressure gauges are popular in environmental monitoring, HVAC systems, and laboratory settings where accurate, low-pressure measurements are essential. They are often used for applications like filter monitoring and airflow measurement in controlled environments.
Digital Pressure Gauge
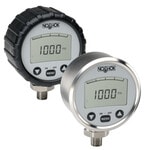
Digital pressure gauges offer a modern solution to pressure measurement, using sensors and electronic components to provide highly accurate readings. Unlike mechanical gauges, digital pressure gauges have no moving parts, which makes them more resistant to wear and tear. They often feature digital displays and can be integrated with data logging systems, making them ideal for applications requiring real-time monitoring and historical data.
Advantages of Digital Pressure Gauges:
- High Precision: Digital gauges provide exact measurements, with some models accurate to within 0.025%.
- Data Logging Capability: Many digital gauges can store readings or send them to a central system, making them suitable for automated processes.
- Easy Calibration and Maintenance: Digital pressure gauges are simple to calibrate and require less maintenance due to their lack of mechanical parts.
Common Applications: Digital pressure gauges are used in high-tech manufacturing, research labs, and industries that require precise pressure control, such as pharmaceuticals. They are ideal for applications where data tracking is essential, or where users need to log pressure readings over time.
Why Selecting the Right Pressure Gauge Matters
Choosing the right pressure gauge is crucial for maintaining safe and efficient operations. Different types of gauges offer unique features suited to specific applications, from high-pressure environments to low-pressure gas monitoring. Understanding the strengths and limitations of each gauge type allows professionals to make informed choices, ensuring accurate measuring pressure across diverse industrial settings.
- Bourdon Tube Gauges: Ideal for robust, high-pressure applications.
- Diaphragm Gauges: Perfect for low-pressure and corrosive media.
- Capsule Gauges: Suited for precise low-pressure gas measurements.
- Digital Gauges: Excellent for high-precision, real-time monitoring.
Explore Our Pressure Gauge Solutions
At AMS, we recognise the importance of accurate pressure measurement, which is why we offer an extensive selection of high-quality instruments, including absolute pressure gauges, differential pressure gauges, and vacuum gauge options. Our range also includes specialised devices for differential pressure measurement, as well as pressure switches for automated systems. Each of our products is manufactured to the highest standards, providing you with reliable and accurate measuring pressure solutions for any industry.
Whether your needs are in mining, food and beverage, pharmaceuticals, or another field, our team is here to help you find the right pressure gauge for your requirements. Contact us today to discuss how our expertise can support your operations, or visit our contact-us page to learn more about our offerings.