
Level sensors are crucial tools for level measurement in a wide range of industrial applications. These devices play a vital role in detecting and measuring the liquid level or solid levels within containers, tanks, or vessels. But what is the process of level sensor, and how does it work? Simply put, level sensors use various technologies to either make physical contact with the material or measure its level remotely using non-contact methods. Understanding these processes is key to ensuring operational efficiency and accuracy in industries such as chemical processing, mining, and food and beverage.
Overview of Level Sensing Technologies

Level sensing technologies are broadly classified into contact sensors and non-contact sensors:
- Contact sensors: These physically interact with the material being measured. Examples include:
- Float level sensors: Using a mechanical float to measure liquid levels.
- Conductive sensors: Employing electrical conductivity to detect levels in conductive liquids.
- Non-contact sensors: These measure levels without physical interaction. Examples include:
- Ultrasonic level sensors: Using high frequency sound waves to measure liquid levels.
- Radar level sensors: Employing microwave signal reflections for precise measurements.
Additionally, these technologies can be further divided based on their functionality:
- Point level sensors: Indicate whether a material has reached a specific level.
- Continuous level measurement: Provide ongoing data about material levels as they rise and fall.
Step-by-Step Process of How Level Sensors Work
Each type of level sensor operates differently depending on its technology. Below is a breakdown of how key types function:
- Ultrasonic sensors:
- Emit high frequency sound waves towards the liquid surface.
- Measure the time it takes for the sound wave to return after bouncing off the liquid.
- This time delay helps calculate the distance and determine the level.
- Radar level sensors:
- Transmit a microwave signal to the liquid.
- Measure the time taken for the signal to reflect back to the sensor.
- Suitable for measuring levels in high pressure, dusty environments, or with corrosive liquids.
- Float level sensors:
- A mechanical float rises or falls with the fluid level.
- The float’s movement triggers a sensor output signal, indicating the level.
- Capacitance level sensors:
- Detect changes in the dielectric constant between two conductive plates.
- The presence of a material (solid or liquid) changes the capacitance value, allowing for level detection.
- Hydrostatic pressure sensors:
- Measure the hydrostatic pressure exerted by a liquid column.
- This pressure is directly proportional to the liquid level.
These processes ensure highly accurate measurements across diverse applications, making level sensors indispensable in modern industries.
Why the Process of Level Sensors Matters
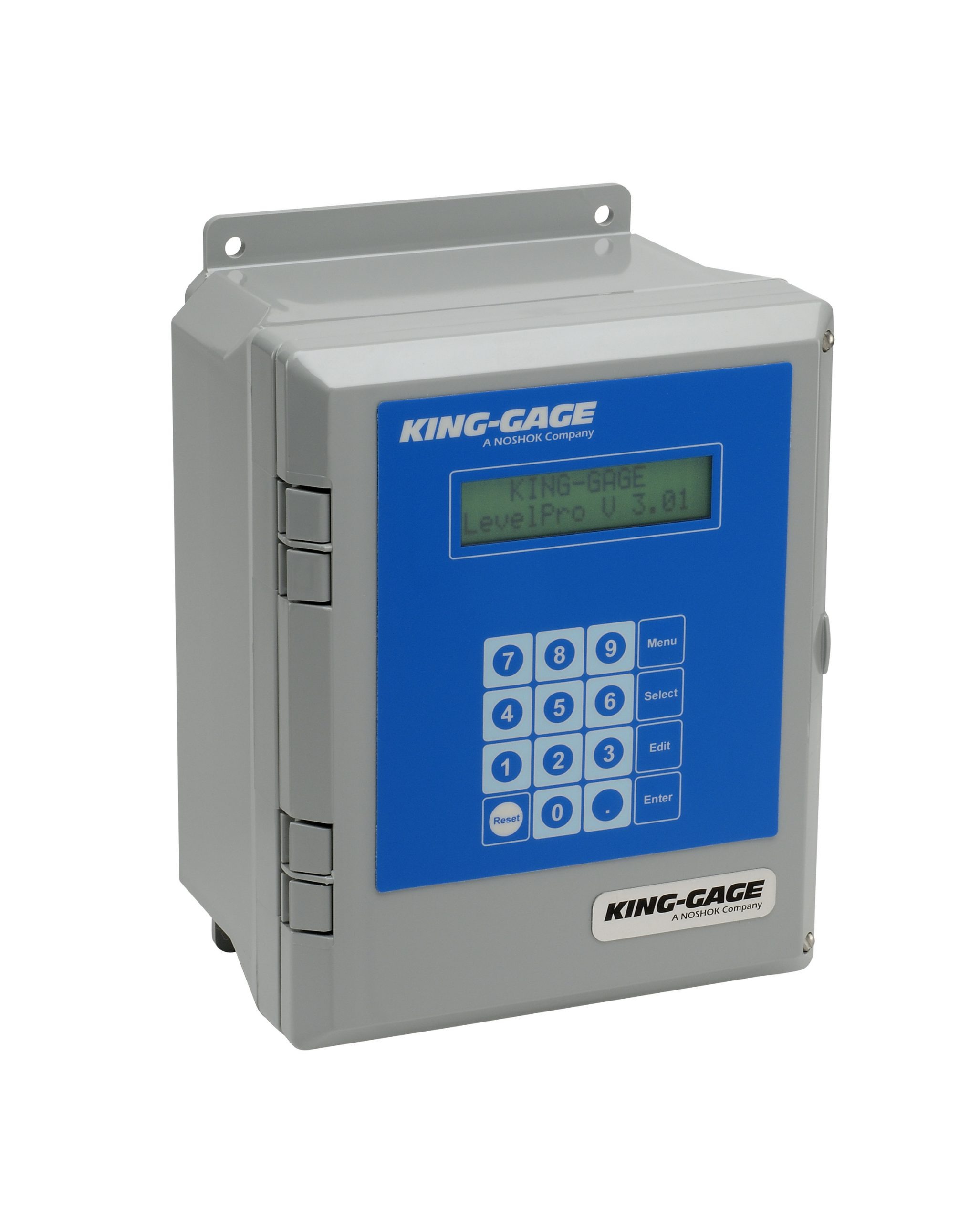
Understanding the operational process of level sensors is critical for optimising process control and improving operational efficiency. Here’s why it matters:
- Accuracy in Industrial Applications:
In industries like chemical processing and food processing, precision is vital for maintaining quality and safety. Level sensors ensure that tanks and containers maintain the correct levels of liquids or bulk solids, avoiding overflows or shortages. - Enhanced Safety:
Accurate level monitoring minimises risks associated with equipment failure, especially in environments with high pressure or high temperature. For example, detecting levels in tanks with highly corrosive liquids can prevent catastrophic leaks. - Improved Efficiency:
Non-contact sensors like ultrasonic level sensors enable measurements without interfering with the process, ensuring uninterrupted operations even in challenging conditions such as dusty environments or environments with foam. - Tailored Solutions for Specific Needs:
Different applications require different sensing technologies. For instance:- Radar level sensors excel in high frequency applications.
- Float level sensors are cost-effective and ideal for simple setups.
- Capacitance level sensors work well in both solids and liquids, offering versatility.
Common Challenges and AMS’s Solutions
While level sensors offer immense benefits, they can face challenges such as interference from environmental factors or the need for calibration. At AMS, we provide solutions designed to address these challenges:
- Non-contact sensors for difficult environments, such as those with foam, vapour, or turbulence.
- Properly calibrated contact sensors for applications requiring direct interaction with the process fluid.
- High-precision instruments designed to handle corrosive liquids, bulk solids, and other demanding materials.
Our range of level sensing technologies ensures reliability, accuracy, and adaptability, making them the perfect choice for various industrial applications.
AMS – Your Trusted Partner in Level Sensing
Precision in level measurement is more than just a technical requirement—it’s a business advantage. At AMS, we specialise in providing state-of-the-art level sensors tailored to your industry’s unique needs. Whether you require solutions for chemical processing, water treatment, or food processing, we have the expertise to deliver highly accurate and reliable results.
Experience the AMS difference today. Visit our contact-us page to learn more about our cutting-edge solutions and how we can support your operational success.