Essential Factors For Sizing A Pressure Gauge Relative To Process Pressures, Normal Operating Pressures And Maximum Pressures
Pressure gauges are an essential component of any process system as they provide a vital indication of the system’s pressure, which is necessary for a safe and efficient operation. Choosing the right pressure gauges for the application is critical, and several factors should be considered, including the pressure range, accuracy requirements, and gauge size.
Process pressures in any plant can be either static or dynamic, and selecting a pressure gauge that operates outside the system’s pressure range can cause inaccurate readings, gauge failure or affect the plant operation.
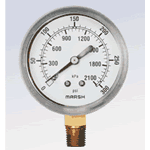
Pressure gauges are designed to operate within specific pressure ranges, typically expressed in pounds per square inch (psi), bar or mm WG. The pressure range should cover the entire normal operating pressure range of the system with sufficient resolution to provide an accurate reading.
It is important to note that the pressure range of a gauge should be a minimum of 10% over the maximum working pressure in static conditions (no pressure fluctuations). In dynamic conditions, the gauge range should be a minimum of 40% over the maximum working pressure. Ideally, the pressure gauge range should be selected for a midscale reading during normal operating pressures.
Normal operating pressures refer to the pressure range in which the system typically operates, and the pressure gauge’s range should cover the entire normal operating pressure range with sufficient resolution to provide an accurate reading. For applications that require high accuracy, it may be necessary to select a pressure gauge with a higher resolution or a lower measurement uncertainty.
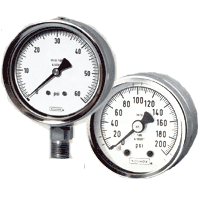
The maximum pressure is the highest pressure that the system can generate, and it’s essential to select a pressure gauge that can safely and accurately measure the system’s maximum pressure. The pressure rating is the maximum pressure that the gauge can safely withstand without failure. It should be higher than the system’s maximum pressure to ensure that the gauge can withstand any pressure spikes that may occur during the system’s operation.
When sizing a pressure gauge, it’s also important to consider the gauge size. The size of the pressure gauge should be appropriate for the applications required accuracy, and the system’s location. How accurately you need to read the pressure value should be a factor when selecting the correct gauge. A larger gauge may be required for systems that require higher accuracy are difficult to access or have high vibration levels.
These factors are to be considered when choosing a pressure gauge to ensure the safe and efficient operation of the process system.
Multiple connection options are available from Noshok to suit many applications including panel mount. A wide variety of pressure ranges, scale options, connections sizes, and options including flanges, case options, cover rings, lens materials, pointers, and orifices are also available.
AMS-IC and Streat Control (NZ) are the distributors of the Noshok range in Australia and New Zealand NOSHOK, Inc | Measurement Solutions
If you require any further information contact Dave Gray dave.g@ams-ic.com.au to assist you with any further information.