Application Background
Within the power generation industry, it is common practice to use hydrogen as a direct coolant for the generator stator windings. Hydrogen is used because it has an extremely high heat transfer capacity – it is much more efficient at transferring heat than any other medium.
The re-circulating hydrogen removes heat from the generator, transferring it, via a heat exchanger, into a secondary cooling circuit which uses de- mineralized water. Often this de-mineralized water is then cooled either by sea water or river water, dependent upon the location of the power station.
As it is not possible to hermetically seal the generator set casings there is the potential for moisture to ingress from the surrounding air. Similarly, as the heat exchanger gradually becomes more porous with age, it too will allow moisture to get into the hydrogen. So it is important that the circulation loop for hydrogen gas on such an installation should include a desiccant dryer, to continuously remove absorbed moisture. The greatest fear, should moisture be allowed to build up in the hydrogen, is that condensation will occur on exposed live metal parts – leading to the risk of flashover. On generator sets which typically produce 22 kV at 19,000A, this could be disastrous. It is therefore recognised practice within the industry that the dew point of the hydrogen gas leaving the generator set should be maintained at a safe margin below the minimum casing temperature, typically an upper limit of 0 °C dew point at system pressure is observed. Should the hydrogen dew point rise above this upper limit, it is important for immediate action to be taken – either to decommission the generator to a a repair or more likely to take immediate remedial action by pumping fresh, dry hydrogen into the system.
Read more about Michell Instruments
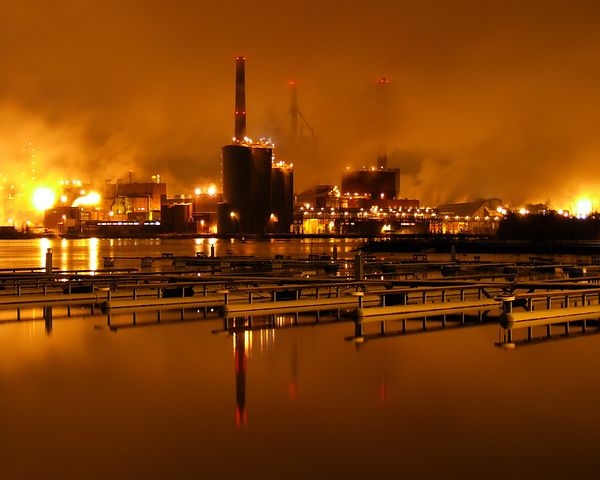