In many of the food industries the process of clearing the equipment and pipes between batches or between products is essential. In the past conductivity systems have been ‘tricked up’ to provide a ‘suitable’ output. However, where water is flushed through (pushed through/push outs) between products, or when product is re-introduced, this is where conductivity has often let you down because there is little difference between the two liquids (water and product) and the temperature is changing. Changing temperature also confuses a conductivity system.
Likewise, in some of your processes there are no measurements of the interface, the determination of interface is made using timing circuits. In timing style of operation valves are closed or opened, then ‘count to ten’ before opening or closing another. This to, by design, needs to ensure that the interface is well past the drain point before being diverted back into the process. If your pumps and valves are now ‘different’ to the day you set them up, then your timing is out and so is your process.
The ideal solution watches the interface and reports what it sees. In this style of process monitoring neither product quality is reduced or is products lost and your emissions (water/product or product/product) are kept as low as necessary.
Interface Detection / Phase Separation.
Into your scenario let’s inject a system that, as we said, ‘watches’ the process and sees the interface pass. Clearly that, must improve your process control?
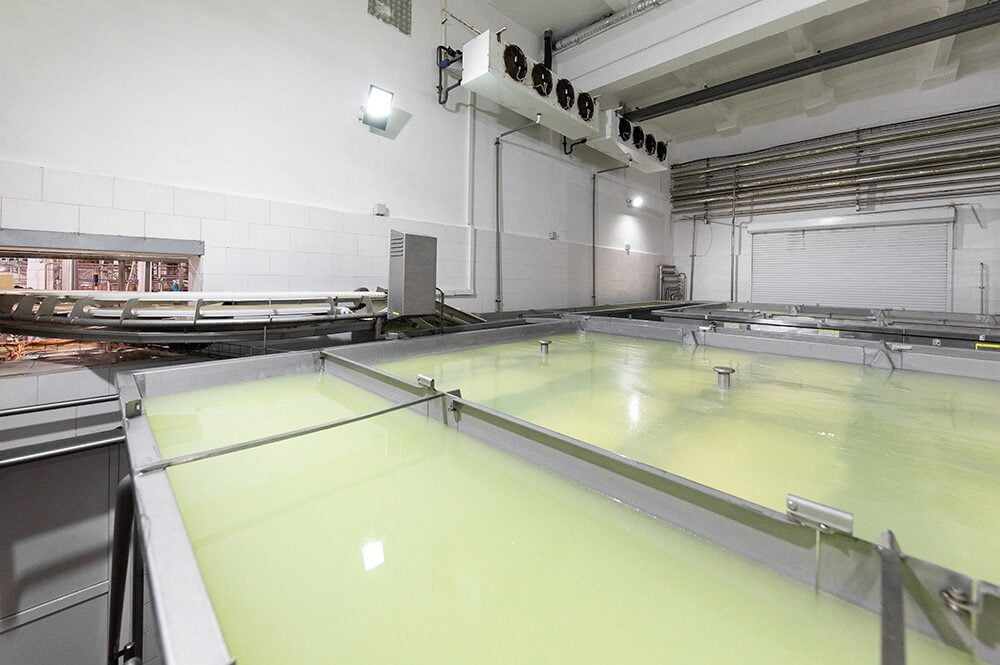
Precise process interface detection with a single channel absorption photometer (optek AS16 or AF16) is the easiest and most effective technique available to food and beverage processors today to reduce product losses.
For a large food production facility, the sheer number of change-over/push out operations can cost thousands of hectoliters of product and by-products each week. In today’s economy, maintaining as much product as is possible is essential to maintain a profitable business.
Keeping the product in production is only one part, the costs go beyond the product alone. Water as the push-out medium is also a commodity and has an inherent cost to procure and to pre and post treat. Product and water going needlessly down the drain are large contributors to plant effluent and the costs to treat it. Local municipalities may also be involved: applying charges to the volume of effluent and even fines if solids load or BOD limits are exceeded. Gaining control of plant interface functions not only makes sense, it’s also environmentally friendly.
Increased Product Quality
Product losses are no longer an issue when detecting different products inline. Faster product changeovers are possible with continuous optek inline measurements. There are certain advantages inline photometers provide over traditional conductivity measurements.
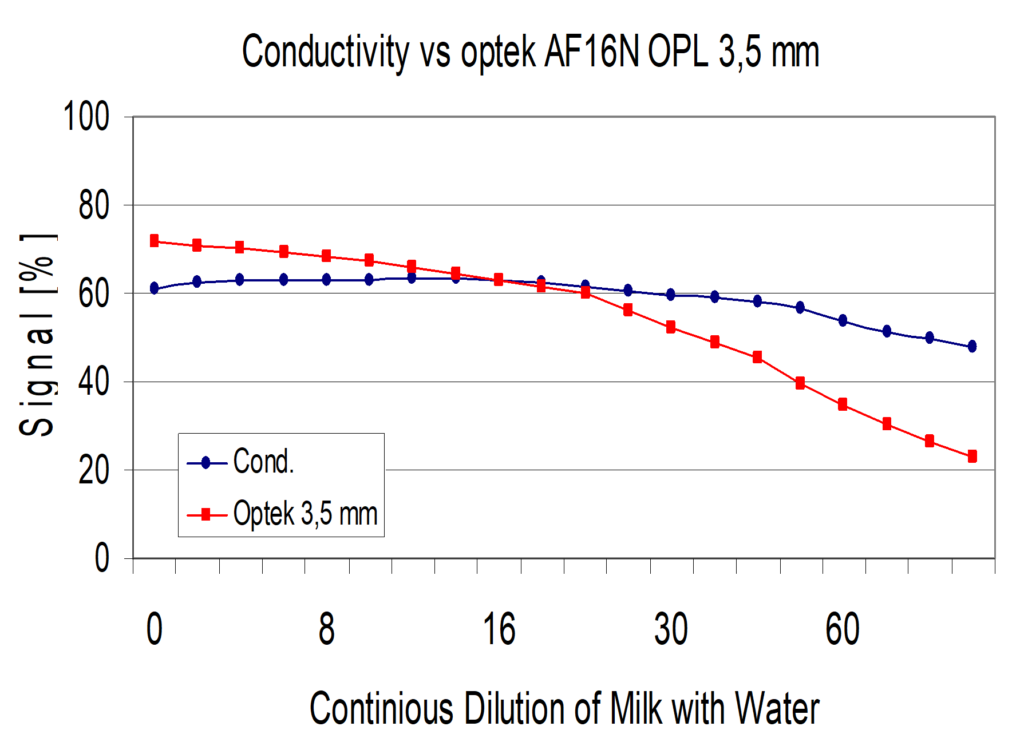
In the chart above, you can see the conductivity of the water/milk interface is almost flat until a significant amount of water is present. The Optek output is significantly more defined with even small changes in water content having measureable change in reading.
What are the benefits of Optek in this type of application? These include fast response time and excellent repeatability in the use of relays for automatic diversion, resulting in higher product quality and improved process control.
In this type of application the savings can be calculated. Calculation of savings is based on the number of product changes/push outs per day and the savings of product per push out. For example if you are flowing in a 50mm line, at 1m/s (120lpm), 3 seconds worth of savings will potentially save 6 litres of product per changeover/push out. In your process, multiply that by the number of changeovers per day, by the number of days operating per year and by the cost of the product per litre.
AMS can provide you with prices for various systems to suit your needs. Overall Return On Investment (ROI) for some users has been in weeks, while for others it has been months. Whatever the payoff time, the savings start from day one and, as a benefit there is greater insight into what is happening in real time.
AMS/Optek solutions vary depending on specific needs. The simplest would include an insertion probe and an analogue converter, working as a one on one. For larger systems there is a digital converter with sophisticated communications and capabilities along with the ability of connection up to 4 probe or flow through sensor into the one system. AMS offers customized solutions based on your process media and automation requirements. Using optek you can also manage phase separations in a wide range of wavelengths, from ultraviolet (UV) to visible (VIS) and near-infrared (NIR).
The application of optek photometric analysers fit in many Dairy and food applications. We would be happy to discuss this application and others with you!
Isn’t time to be more Analytical!
- For further information you can also contact our Product manager – Peter Sims
- https://www.ams-ic.com.au/product/optek-danulat-process-control-solutions/