Service companies that perform calibrations for the process industries operate in a challenging environment. Not only is there a lot of competition, but contracts for customers are based on estimates, meaning that every additional hour of work directly affects the bottom line. Finding and retaining skilled calibration technicians is also a challenge.
So, what can service companies do to make their quotations more accurate and ensure work is carried out as consistently and efficiently as possible? The answer is to automate the calibration process.
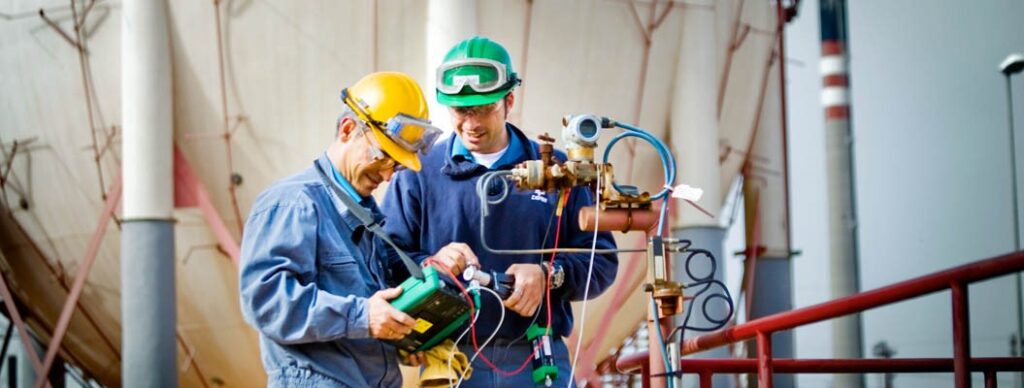
The problems with pen-and-paper calibration
To see why automation helps, first we need to look at the way calibrations are currently conducted using pen and paper. Paper-based calibrations are time consuming, with 40–50 data points needing to be filled in by hand for each calibration. Because it relies on manual data entry, paper-based calibration is also prone to errors. It’s commonly accepted that the typical error rate in manual data entry is around 1%. While this might not sound like a lot, it can have major implications for the accuracy of the calibration process. The end result of manual processes is that every second calibration certificate might possibly contain an error.
Paper certificates also negatively affect transparency – when using them, it’s hard to share calibration results with end customers in a timely fashion. Paper certificates also require warehousing and are not easy to find when an audit is required – let alone if the client wants to use the calibration data improve their process efficiency through trend analysis.
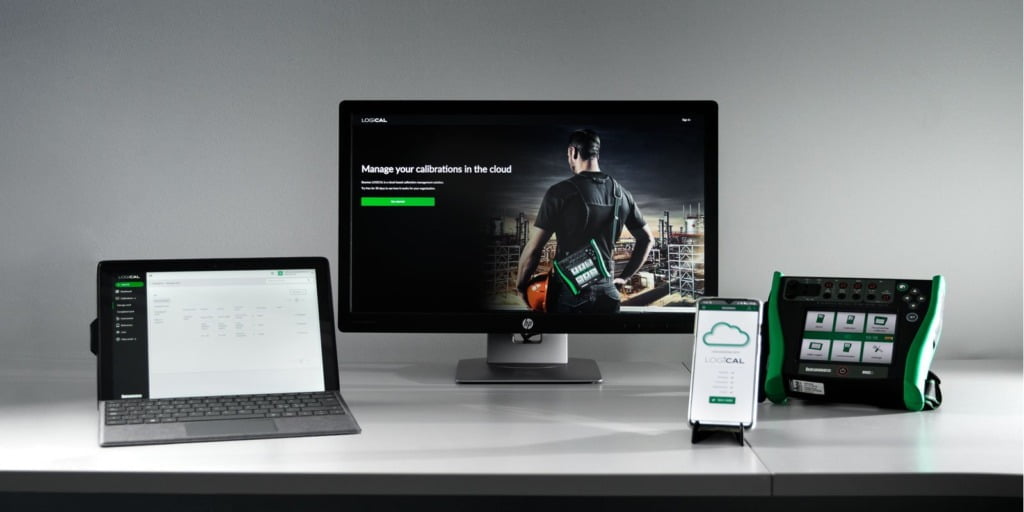
You can go paperless today
Beamex’s automated calibration solution combines software, hardware, and calibration expertise to deliver an automated, paperless flow of calibration data with a minimal requirement for manual data entry. The major benefit here is that an automated process cuts the number of steps involved in the calibration process, potentially saving up to 50% of the time it takes. Even shaving just 15 minutes off the time needed to perform a calibration, plus an additional 15 minutes due to not having to manually enter results into a database, adds up to huge time savings.
In addition to saving time and enabling a more efficient process, automated calibration helps to avoid mistakes typically associated with manual data entry – thus improving the quality and integrity of the calibration data and making sure your customers are happy with the work you’re doing for them.
Modern multifunction calibrators from Beamex also provide user guidance so that even less experienced technicians can carry out calibrations quickly and reliably. Because the process is highly repeatable, making quotations becomes easier as you will know how much time is needed for each calibration.
Finally, with automated calibration you can offer your customers new services based on data analysis. Because all the calibration data is in a digital format and easily searchable, you can analyze your customers’ calibration processes and data to provide improvement recommendations – differentiating your service company offering.
The commercial arrangements for the project are designed to lower client risk. At the start of the project, an eight-week Data as a Service (DaaS) contract is agreed.
A decision to return equipment or extend the contract is made at the end of the 8 week period. The project team has the option to extend the agreement from 6 months to 5 years at lower monthly fees. DaaS agreements include all software updates, support and warranty. If, at any time, the system uptime is less than 90% of any particular month (due to hardware, software or other issues within the control of Process Vision) the DaaS service is free for that month
Example of ROI calculation (Sample only)
The average cost to a service company for an instrument technician is around $75 per hour, including salary, benefits, overheads, and so forth.
If a technician carries out 2,000 calibrations a year and it takes them on average 15 minutes to write up a calibration certificate for each calibration, then writing certificates costs a service company $37,500 per year per technician.
Assuming it takes another 15 minutes to manually enter that data into the database, then entering data costs another $37,500 per year per technician.
Automating this process would save 1000 hours of work per year per technician and result in significant cost savings.
For further information you can also contact our Product manager – Mike Farkas mike.f@ams-ic.com.au