Oxygen is the most common naturally occurring element on earth and, after hydrogen and helium, the third most common element in the universe. It is generally thought that oxygen levels in the earth’s atmosphere only began to increase around 2.3 billion years ago due to photosynthesis in ancient bacteria and plants. You then need to fast forward to the eighteenth century before oxygen was first correctly identified by three scientists working independently: the Englishman Joseph Priestley, a Swede called Carl William Scheele, and a Frenchman, Antoine Lavoisier. It was the last of these who gave the gas its name, calling it oxy-gene, which means acid-forming, as he thought that it formed the basis of all acids.
Today, we know that oxygen has an atomic number of 8 (meaning it has a nucleus containing 8 protons) and that oxygen atoms combine in pairs to form the molecule O2, which is essential for the respiration of most living beings. Oxygen and its compounds comprise about two-thirds of our bodies and around half of the earth’s crust.
Oxygen is critical to life and an important element in many industrial processes, from steel production to additive manufacturing, brewing, and fish farming.
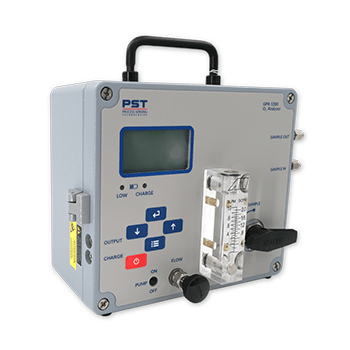
How is industrial oxygen produced?
Oxygen for industrial, commercial, and medical purposes is normally produced using an oxygen generator. There are several different types, each designed for specific applications and operating conditions:
Pressure swing adsorption (PSA) oxygen generators. They pass atmospheric air through a bed of zeolite molecular sieves, which adsorb nitrogen, allowing oxygen to pass through and be collected.
Vacuum Pressure Swing Adsorption (VPSA) Oxygen Generators: These are similar to the above, but a vacuum is used to desorb nitrogen from the molecular sieve.
Membrane Oxygen Generators. These devices use semi-permeable membranes that selectively allow oxygen to pass through while retaining other gases.
Electrochemical Oxygen Generators: Electrochemical cells are used to produce oxygen through the electrolysis of water.
Chemical Oxygen Generators: These generators produce oxygen through a chemical reaction, typically by heating a compound such as sodium chlorate.
Cryogenic Oxygen Generators: These operate by liquefying and distilling air to separate oxygen from nitrogen, with the former being re-gasified before use.
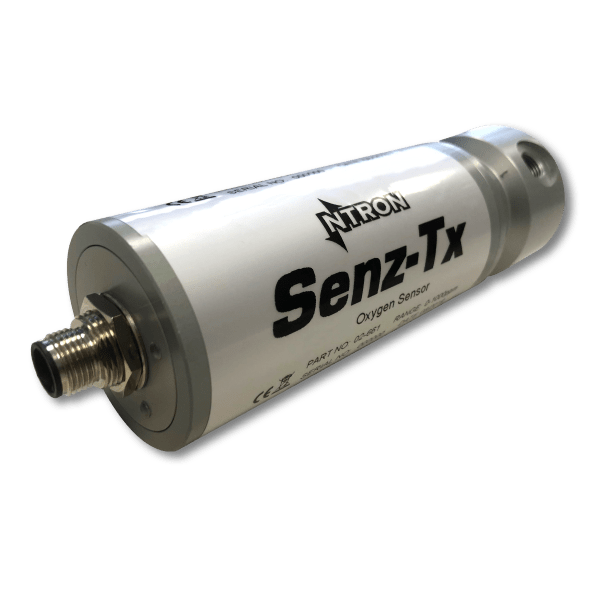
Gas quality, generator efficiency, and safety
Regardless of which type of oxygen generator is used, there is a common need to ensure that the quality or purity of the gas produced matches the required standards while ensuring each generator functions efficiently and safely.
This is normally achieved by using specialized oxygen monitoring instruments, using either electromechanical or zirconia-based sensing mechanisms. These can produce extremely accurate and consistent results at oxygen concentration levels of just a few parts per million, with a fast response to changing process conditions.
Electrochemical sensors function by measuring the current generated by a chemical reaction taking place between oxygen molecules in the process gas sample and a specialized electrolyte in the sensor. The current is directly proportional to the concentration of oxygen, providing a fast, simple and accurate reading.
By comparison, Zirconia-based oxygen sensors use the conductivity of zirconium dioxide to Oxygen when at a high temperature. The sensor measures the difference in oxygen concentration between the gas presented to the sensor and a reference gas, typically ambient air, from the oxygen ions movement through the zirconia.
Industry-leading oxygen analyzers
PST have been manufacturing industry-leading oxygen analyzers for many years. Our latest product range offers the option of electromechanical and zirconia sensors, giving customers a choice of technologies, depending on their application requirements. For example, zirconia sensors provide fast response times with almost zero drift and a long service life, while electrochemical sensors allow measurement in background gases containing hydrocarbons.
In each case, our Microx , SenzTx, et GPR ranges of analyzers are simple to install, configure, and operate. They are available in various configurations, including DIN-rail, panel, and wall mount, with remote sensors and a wide choice of process connections. The SenzTx also comes with a range of process connections, including Flow-through and KF40 Flange. In common with all our products, the Microx, SenzTx, and GPR analyzers are backed by comprehensive worldwide technical support and customer services.
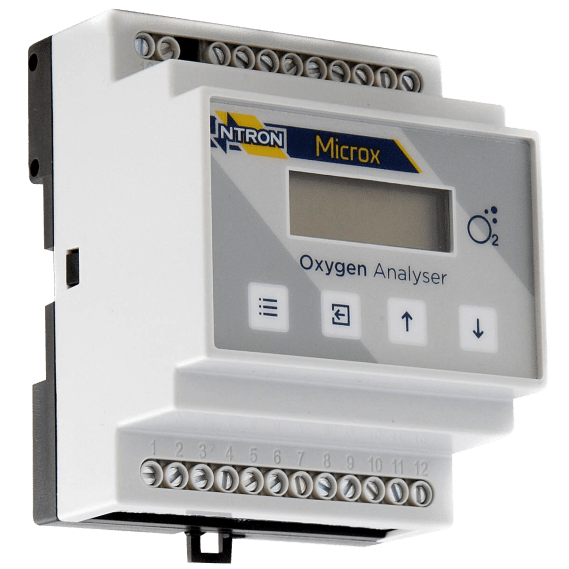
Did you know?
The performance of an oxygen analyzer will be determined both by its design and the quality of installation. For example, the speed at which the analyzer responds to changes in process conditions will be affected by the length of the gas path, how far the sample gas has to travel before it reaches the sensor chamber, and the flow efficiency of the chamber itself.
As a leading manufacturer of oxygen analyzers, we pay close attention to the design stage to ensure that the internal gas flow paths are optimized to produce the fastest results without compromising accuracy. It is, however, equally important to minimize the distance that the gas must travel from the point of sampling back to the analyzer. Additionally, it is essential that any pipework connections are carefully checked to ensure that there can be no air ingress through leaking flanges or glands, which would adversely affect the quality of subsequent readings.
Contact Dave Grey dave.g@ams-ic.com.au , our analytical product manager today to discuss how our expertise can support your requirements, or visit our contact-us page to learn more about the analytical range of instrumentation.