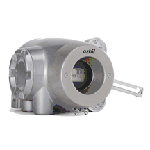
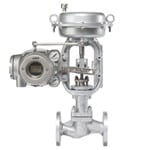
Brazil is the world’s largest sugar-producing country. It has strong economic ties with Japan, with many Japanese companies doing business in Brazil. Usina Coruripe was founded in 1925 in the city of Coruripe on the southern coast of state of Alagoas in Brazil. As it expanded its sugar production business, Usina Coruripe also began producing ethanol from sugarcane for use as automobile fuel, and is now one of the 10 largest companies in Brazil in sugar and ethanol production. In addition, the company generates power from biomass, an eco-friendly energy source, mainly for running its own plants.
One of the company’s main plants, the Campo Florido Unit, can process 4.4 million tons of sugarcane annually. The produced sugar is sold not only to domestic and overseas markets, but also under Coruripe’s own brand, which is distributed mainly for household use in Minas Gerais, Alagoas, and other states.
The Campo Florido Unit’s sugar and ethanol production processes include fermentation, processing of the remaining material after stripping and crushing sugarcane, drying, evaporating, crystallisation, and refining. In the past, the positioners that controlled the valves for various processes often malfunctioned, with a high probability that repair would be needed. Usina Coruripe has a number of factories with similar production processes at various domestic locations, so the challenges it faced affected the entire company.
“Every time we had a breakdown, we had to shut down the plant, lowering its availability factor. So we tested positioners from multiple manufacturers to find a cost-effective product with fewer failures,” says Electricity and Automation Maintenance Coordinator Wilson Angelo de Menezes Junior.
Selecting a reliable product to improve productivity and reduce workload
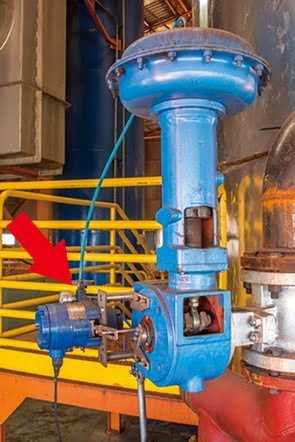
In the examination of many manufacturers’ positioners, the quality and cost effectiveness of Azbil Corporation’s smart valve positioners became apparent through actual demonstrations. The plant utilises valves made by a number of manufacturers, both Brazilian and foreign. If a positioner fails, the company must ask the manufacturer for repair, which is a heavy burden on the maintenance site. Azbil’s smart valve positioner received high marks for its compatibility with various manufacturers’ valves of differing specifications used at Campo Florido, as well as for its quality and cost-effectiveness. Azbil’s positioner was selected in June 2018. In July of the same year, smart valve positioners and 10 sets of mounting plates for installation on other companies’ valves were delivered, and the positioners began operation.
“Although we do our best to improve the quality of the plant instrumentation air, we cannot completely prevent contamination by water and oil. In operating Azbil’s positioners*, we found that they continue to operate without failure better than other manufacturer’s positioners,” says Wilson Angelo de Menezes Junior.
In addition, the installation and adjustment of positioners differ depending on the valve manufacturer, so with many brands of positioner the operators must learn many different procedures. However, since Azbil’s positioners can be mounted on any manufacturer’s valve, it is now possible to handle all valves by learning just one installation procedure and adjustment procedure.
“If positioners are standardized throughout the entire plant, we can reduce the workload on the staff. Azbil’s positioners are less likely to break down, are easier to maintain, and put less of a burden on the staff. Although it has only been a year since they were installed, they have earned a high level of trust,” says Instrumentation Supervisor Cacinildo Silva.
Not only have repair costs been reduced, thanks to the elimination of failures, but also the standardization of positioners has made quick replacement work possible. As a result, the time required to stop the plant has been shortened, and the plant’s availability factor has improved.
“The most important thing is that the equipment continues to operate. For that purpose, a situation in which no products fail is a must. Sugar and ethanol production processes run for 7 to 8 months, leaving a 4 to 5 month outage for regular repairs. If the equipment stops due to a positioner problem during the 7 to 8 months of operation, production efficiency is greatly affected. By changing to Azbil’s positioners, we were able to increase availability and production efficiency,” says Plant Manager Geovani Araujo da Silva.
For further information you can also contact Dave Grey dave.g@ams-ic.com.au